Diatool’s expertise in the production and development of high performance reamers has led them to create multiple innovative solutions for reaming slip yokes. With a focus on maintaining proper sizing and consistent machining results, a Diatool high performance reamer is the ideal solution when manufacturing yokes.
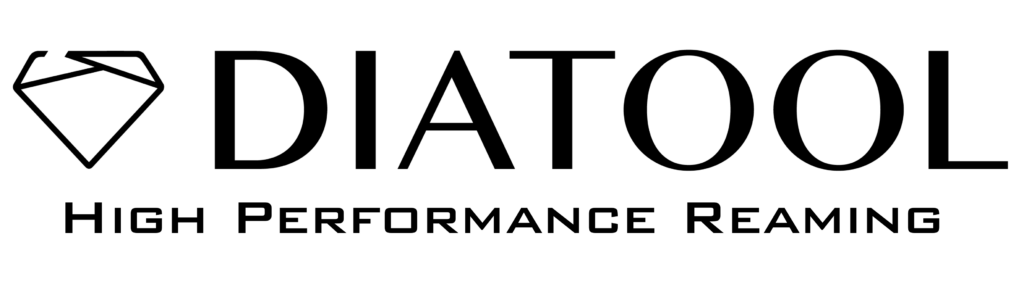
High Performance Reaming Solution
When machining yokes, holding the correct diameter and reducing cycle time are the goal. A reamer with multiple cermet tipped cutting blades provides wear resistance and stability.
Every reamer is designed to maximize efficiency within the specific yoke application parameters. If the yoke is made from a material where chip evacuation is a problem, the reamer can be made with a chip breaking geometry.
Each Diatool reamer comes set to size and ready to cut, requiring no operator adjustment.
- Cermet blades are used which allows for faster cutting speeds and reduced tool wear
- Each reamer's geometry is optimized for the specific yoke application
- Long flutes create stability when exiting the back of the bore to eliminate chipping
- Reaming eliminates alignment issues that are common when boring
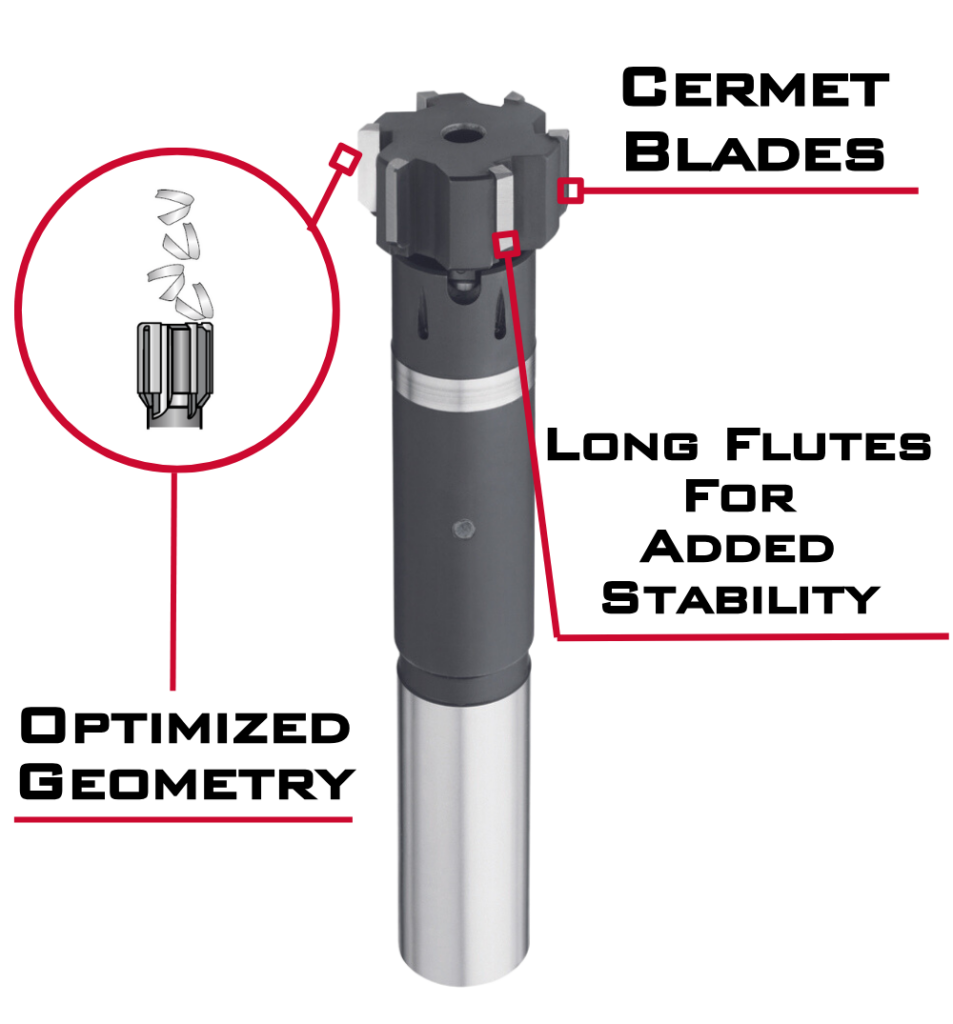
Application Information
- Bores in yokes typically fall within the size range of 1" to 3", but Diatool can handle diameters as small as 5/8" and beyond 3"
- Tolerances achieved in machining these bores are typically within +/- 0.010mm and (+/- 0.0003in), although exact tolerances depend on the diameter
- The most common materials for yokes are ductile iron and medium carbon steels
- Surface finish requirements are not as critical since a bearing is pressed into the bore
- Yokes are a high volume application. With EAU's upwards of 50,000 parts
Common Yoke Machining Challenges
Maintaining consistency within the bore diameter is the main challenge when machining yokes. Traditional methods like single point boring bars wear quickly, leading to inconsistencies. Additionally, boring bars require a time consuming setup.
Chip control can present challenges in yokes made out of materials such as stainless steel. The high volume nature of these parts means that automation is often part of the machining process. Chips wrapping and balling up can create significant issues for robot loaders and tool changes.