Challenge Details
- ∅1.004" bore on a railroad tie puller part
- Material: 4140 hammer forged steel
- Machine: Haas Vertical Mill
- Volume: 2,000 EAU
- Struggled to maintain bore size
Objective
Replace single point boring with a more stable process machining a railroad tie puller part. The goal was to increase tool life and hold size without the need for operator adjustment.
Previously, a single point boring process was used resulting in poor tool life and the constant need to make size adjustments.
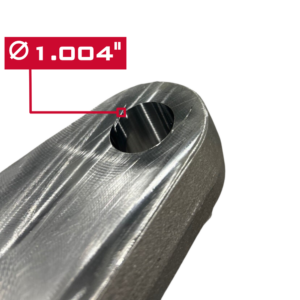
Solution
The Diatool team recommended a ∅25.367mm diameter Diatool non-expandable cermet tipped monoblock reamer with straight flutes and G01 bevel lead. The reamer ran at 1500 RPM and cut 60 IPM. The Diatool reamer came set to size and ready to cut on the first part.
Benefits Realized
Cycle Time Saving
10 seconds saved per part & reduced machine downtime.
Hold Size With No Adjustment
Bore size was maintained without need for adjustment.
Consistent Results
Proper size and surface finish were achieved part after part while reducing scrap.