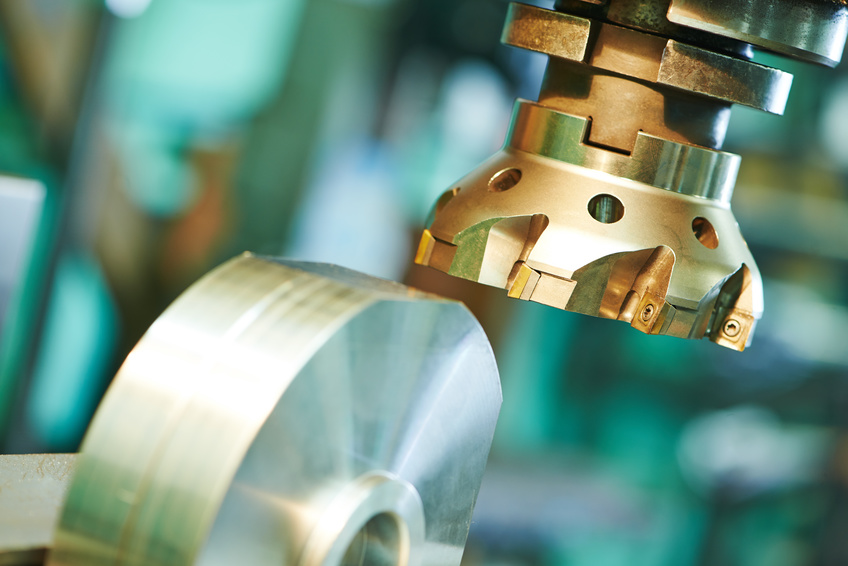
4 BENEFITS TO KNOW ABOUT SOLID CARBIDE TOOLING
When it comes to precision metal finishing and other manufacturing processes like milling and drilling, the materials and tooling you use matter. Solid carbide tools…
Get the latest news, offers, and machining resources from your hole finishing experts by signing up for the Monaghan Tooling Group mailing list:
30 N. Clinton Street
Dayton, Ohio 45402
Toll-Free: 1.800.732.4565
Phone: 937.253.7706
Fax: 937.723.7702
Material: Ductile Iron
Tooling: Rambo Speed Drill with GTX Coating
Advantages:
Material: C70, Steel
Tooling: Drills with S4 geometry (coated) Spotfacing tools, Z=6 (coated)
Advantages: Approx. 3000 holes (drilling)
Material: 42CrMoV4, Steel
Tooling: Special drilling tool with S2 geometry
Advantages: Extended tool life and process stability